CM CANopen for SIMATIC S7-1200
CANopen Master/Slave module for the SIMATIC S7-1200 PLC
The module acts as either a CANopen master or slave device. Alternatively it can work as an ordinary CAN 2.0A node.
Highlights
- Plug-in CANopen Master/Slave module for SIMATIC S7-1200 PLC
- Connects up to 16 CANopen slave nodes in master mode
- 256 byte input and 256 byte output per module
- Connects up to 3 modules per CPU
- LEDs provide diagnostic information on module, network and I/O status
- Integratable in the hardware catalogue of the TIA Portal configuration suite
- CANopen configuration via the included CANopen Configuration Studio Software
- Support for transparent CAN 2.0A for custom protocol implementation
- Pre-made function blocks available for easy PLC programming in TIA portal
- Complies to the CANopen communication profiles CiA 301 rev. 4.2 and the CiA 302 rev. 4.1
- 3 year product guarantee
The CM CANopen module is designed to be plugged directly onto the SIMATIC S7-1200 PLC. The module exchanges data and signals via the backplane bus, which also supplies the module with power.
CANopen support
Simply attach the CM CANopen expansion module to the SIMATIC® S7-1200 PLC. Any device running the CANopen protocol can then be connected. Tthe CM CANopen module can be used from within TIA Portal® and can be configured to be either a Master or Slave from TIA Portal. No programming is needed to create the configuration.
CANopen configuration and TIA Portal integration
The seamless integration into the SIMATIC world is one of the most essential requirements when extending of the SIMATIC automation system with networked fieldbus equipment that is not based on either PROFIBUS or PROFINET. HMS has addressed this need enabling a seamless integration of the CM CANopen module into TIA Portal. Configuration of the connected CANopen network is intuitively performed with the included CM CANopen Configuration Studio.
Once the configuration is finalized, the CANopen network configuration is downloaded into the CM CANopen module and localz stored in non-volatile memory. If one of the slave devices in the connected CANopen network has to be replaced, configuration data for this device will be downloaded automatically by the CM CANopen module once the device is reattached, significantly reducing down-times in high availability applications.
Transparent CAN 2.0A functionality with the CM CANopen
With this functionality, the CM CANopen module allows transmission of any CAN frame from the PLC regardless of the overlaying CAN protocol and is capable of receiving a number of pre-defined CAN frames from the CAN network.
CAN 2.0A supported features
- Possibility to implement any custom CAN based protocol which in interpreted/generated by the PLC
- Special PLC function block available from HMS for easy integration in to TIA Portal
- CAN frames pass transparently through the CM CANopen module
- Ability to transmit and receive CAN frames inside TIA Portal
- Supports only the CAN 2.0A standard (11-bit CAN identifiers)
- Selectable baud rate from 20 kbit/s – 1 Mbit/s
- CANopen functionality is disabled when the transparent CAN mode is used
Technical Data | |
CAN bus interface | According to CiA 303-1 |
Galvanic isolation | |
Power Supply | +5 VDC ±10%, supplied by S7-1200 PLC |
Dimensions | Width 30 mm |
Weight | 120 gram |
Temperature range | Operating 0 ºC ... +60 ºC |
Storage -40 ºC ... +70 ºC | |
Protection class | IP20 |
Certification | CE, UL, cUL & ROHS |
Housing | Plastic housing, plug-in module, DIN-rail mountable |
Contents of delivery |
- CM CANopen module |
- DSUB-9 with screw terminals for CAN-bus |
- Configuration software for Windows™ |
- Configuration cable (USB) |
- User Manual |
Part number(s)
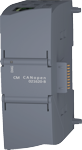